AeroMag™ - Adaptive Electromagnetic Ready‑to‑Print Advanced Magnetics
Ultra‑light 3‑D printable composites delivering high‑frequency power with 35 % less weight.
Overview
AeroMag™ is Reinventy Solutions’ breakthrough platform of soft‑magnetic composite materials engineered for additive manufacturing. By fusing nano‑engineered Fe‑Ni particles with high‑performance binders, AeroMag unlocks true 3‑D flux control, razor‑low core losses, and up to 35 % weight reduction in electric machines.
Why AeroMag™ ?
Tool‑less electromagnetics – print stators, rotors, flywheels, choke cores directly from CAD in hours.
High‑frequency ready – core‑loss as low as 10 W kg‑¹ @ 400 Hz, 1 T (EV‑H) and μr up to 150.
Lightweight efficiency – composite density down to 5 g cm‑³ (filament) vs 7.6 g cm‑³ Fe‑Si; motors up to 18 % lighter at 48 V and 10 % lighter at 400 V.
Thermal stamina – continuous service range 150 °C (EV‑L) to 200 °C (ULTRA‑CORE & EV‑H).
Circularity built‑in – printable lattices cut material mass 30 %; binder reclaim possible at end‑of‑life.
Material Variants
From rapid prototyping to full‑scale electric‑vehicle traction, AeroMag™ now offers five tuned formulations. Compare processes and magnetic performance at a glance, then pick the variant that drives your voltage and power target.
Variant | Printing Technology | Post‑Process | μr (1 kHz, 0.3 T) | Core Loss 400 Hz / 1 T | Density | Notes |
---|---|---|---|---|---|---|
AeroMag‑P | FDM / FFF Filament 60 wt % Fe‑Ni in PC |
2 h @ 125 °C air cure | 90 | ≤ 40 W kg‑¹ | 5.1 g cm‑³ | Ready‑to‑use; print → cure → assemble |
AeroMag‑UV | 405 nm DLP Photopolymer 58 wt % Fe‑Ni |
Rinse + UV + 120 °C 1 h | 100 | ≤ 30 W kg‑¹ | 5.3 g cm‑³ | Surface Ra ≤ 4 µm |
AeroMag‑UV Ultra | Same as UV | Debind + anneal 650 °C N₂ 30 min |
140 | ≤ 20 W kg‑¹ | 6.8 g cm‑³ | High‑power motors (≥ 1 kW) |
AeroMag‑EV‑L™ | FDM Filament 62 wt % Fe‑Si / Ni in PPS | 2 h @ 150 °C air cure | 95 | ≤ 30 W kg‑¹ | 5.1 g cm‑³ | 48 V EV motors λ 0.8 W m‑¹ K‑¹ |
AeroMag‑EV‑H™ | DLP resin + sinter Fe‑Co 64 wt % | Debind + anneal 700 °C N₂ | 150 | ≤ 10 W kg‑¹ | 6.8 g cm‑³ | 400 V traction motors λ 5 W m‑¹ K‑¹ |
Technology in Action
Electronically Clean Interfaces – each Fe‑Ni particle carries a nano‑silicate “H‑layer” insulation, blocking eddy currents up to 5 kHz while preserving high saturation (> 1.4 T).
Smart Rheology – proprietary dispersants keep viscosity below 3 Pa·s (UV) and 300 Pa·s (filament) for flawless 50–150 µm layers.
Scalable Post‑Processing – choose a simple 125 °C air cure for rapid prototyping or an industrial debind‑anneal cycle for maximum performance.
Typical Applications
Drone & eVTOL motors – outrunners 22–40 mm, 10 000–20 000 rpm.
E‑bike mid‑drives & quadricycles – 48 V systems, 2–8 kW.
Passenger‑car traction drives – 400–800 V, 50–150 kW IPM and axial‑flux motors (EV‑H).
High‑frequency inductors – PFC chokes, flyback transformers 100–400 kHz.
Custom actuators – magnetic gears, voice‑coil shells, micro‑gimbals.
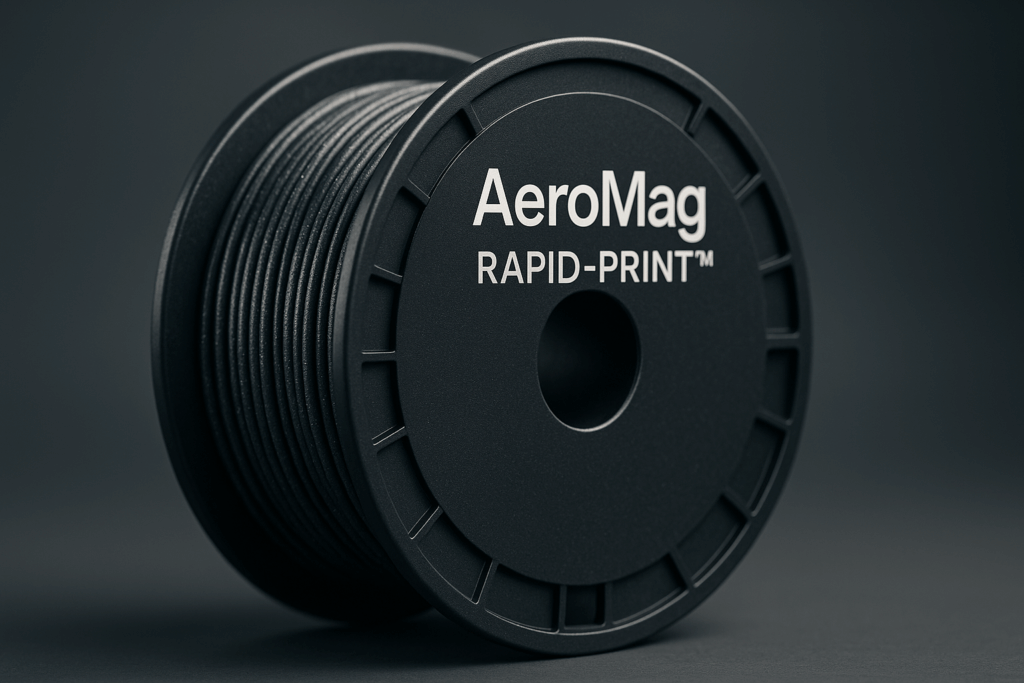
AeroMag RAPID‑PRINT™
Lightweight Ready‑Print Soft‑Magnetic Filament
Description: AeroMag RAPID‑PRINT™ (AeroMag-P) is a 60 wt % Fe‑Ni composite filament (1.75/2.85 mm) in a high‑temperature PC matrix. Print complex stators or choke cores on any enclosed FDM printer, then simply air‑cure 2 hours at 125 °C—no inert ovens, no debinding.
Technical Specifications
Continuous Service Temperature: 145 °C
Magnetic Permeability: μr ≈ 90 (1 kHz, 0.3 T)
Core Loss: ≤ 40 W kg‑¹ @ 400 Hz, 1 T
Electrical Resistivity: 12–18 k µΩ cm
Density: 5.1 g cm‑³
Filament Diameter: 1.75 ± 0.05 mm (2.85 mm option)
Key Applications
Drone & e‑bike motors ≤ 1 kW
High‑frequency inductors (100–400 kHz)
Prototyping 3‑D flux paths & custom actuators
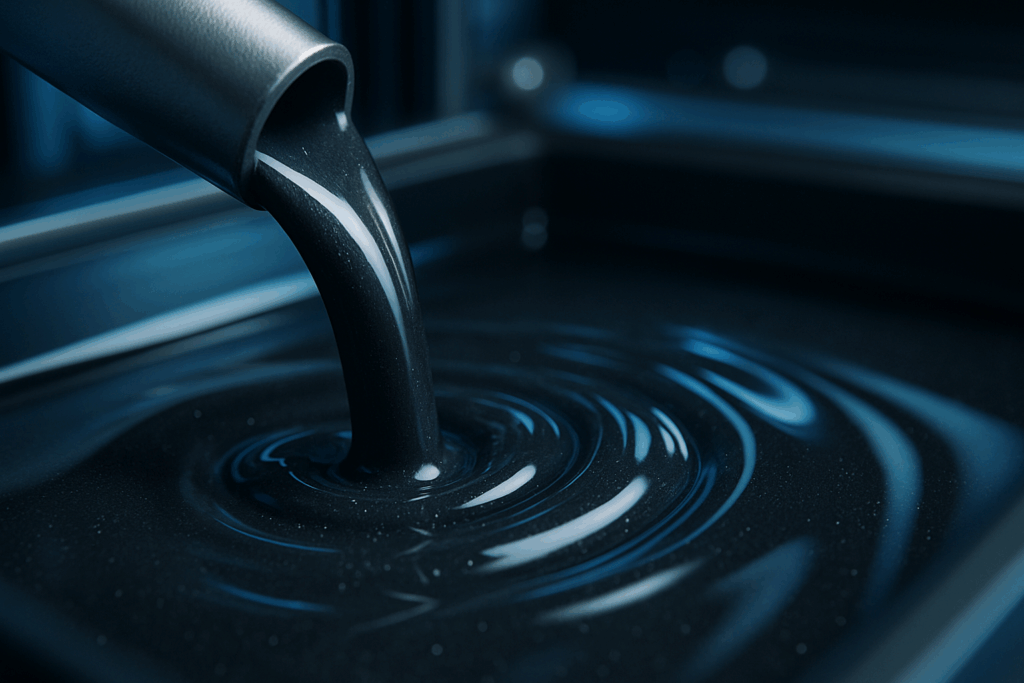
AeroMag DURA‑CURE™
High‑Definition Photopolymer for Precision Magnetics
Description: Formulated for 405 nm DLP/LCD printers, AeroMag DURA‑CURE™ (AeroMag-UV) packs 58 wt % Fe‑Ni into a low‑viscosity resin (2.8 Pa·s). Achieve <200 µm layers, rinse & post‑cure (UV + 120 °C × 1 h) for smooth, ready‑to‑use parts with enhanced permeability.
Technical Specifications
Continuous Service Temperature: 150 °C
Magnetic Permeability: μr ≈ 100
Core Loss: ≤ 30 W kg‑¹ @ 400 Hz
Cure Depth: 200 µm @ 35 mW cm‑²
Density: 5.3 g cm‑³
Key Applications
Micro‑motors, voice‑coil cores, MEMS actuators
Power‑dense PCB inductors & planar transformers
Lattice cooling channels for compact drives
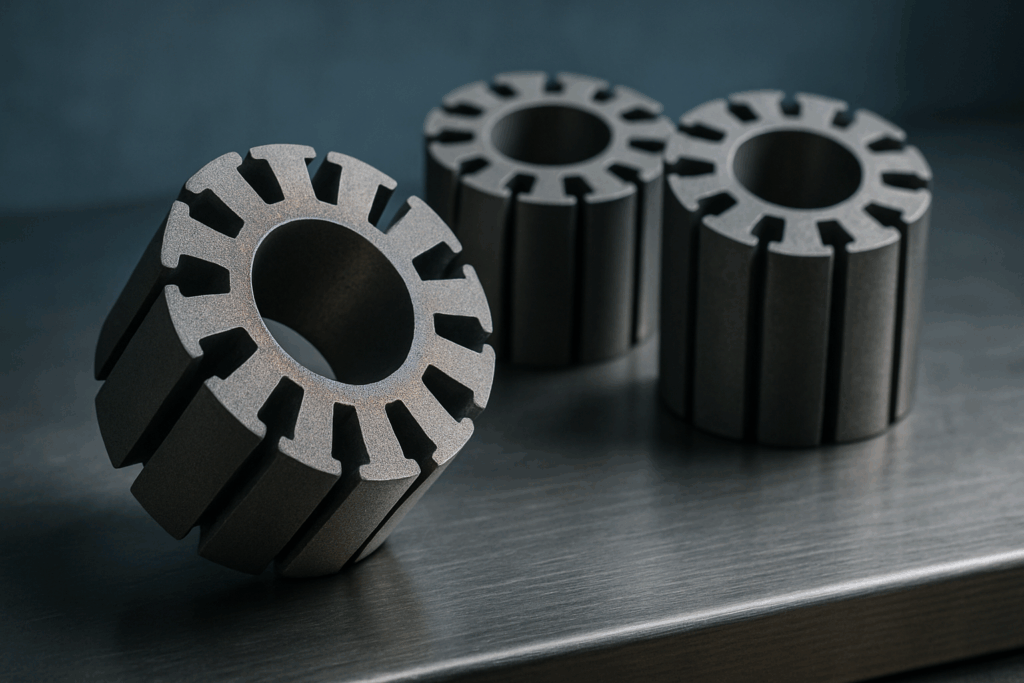
AeroMag ULTRA‑CORE™
High‑Power Sintered Soft‑Magnetic Composite
Description: Starting from the DURA‑CURE™ feedstock, AeroMag ULTRA‑CORE™ (AreoMag – UV Ultra) undergoes a debinding + 650 °C nitrogen anneal, transforming into a densified metal matrix for maximum magnetic performance and thermal conductivity.
Technical Specifications
Continuous Service Temperature: 200 °C
Magnetic Permeability: μr ≈ 140
Core Loss: ≤ 20 W kg‑¹ @ 400 Hz
Density: 6.8 g cm‑³
Thermal Conductivity: ≈ 5 W m‑¹ K‑¹
Key Applications
High‑power ≥ 1 kW e‑drives & generators
Liquid‑cooled stators & axial‑flux machines
Aerospace actuators requiring 200 °C duty
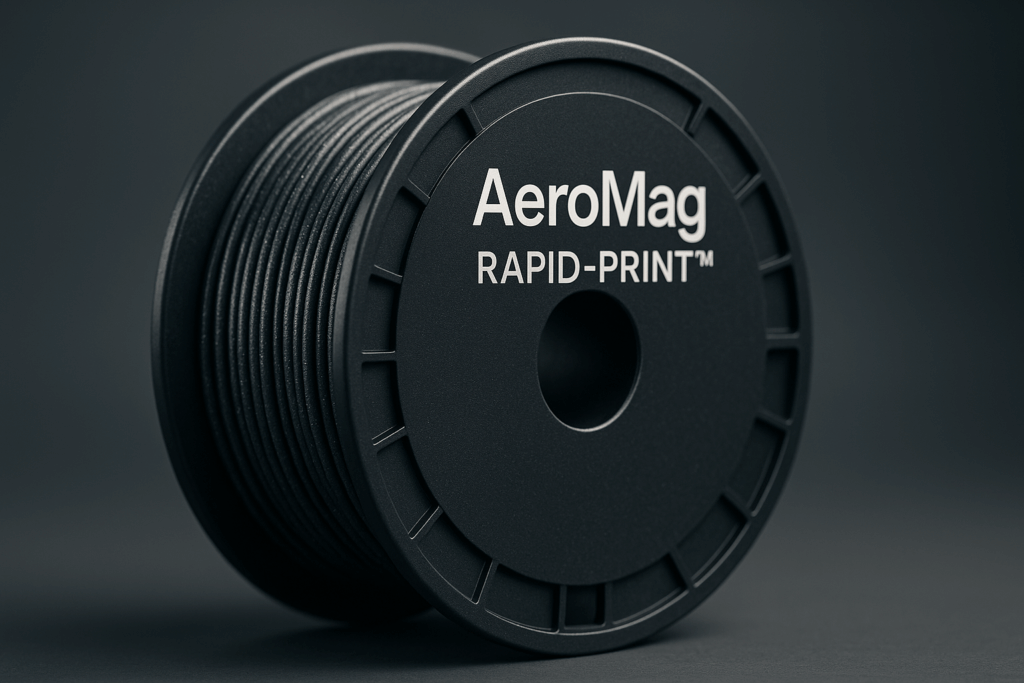
AeroMag EV‑L™
Light‑Voltage EV Filament for 48 V Drives
Description: AeroMag EV‑L™ builds on RAPID‑PRINT technology with a 62 wt % Fe‑Si / Ni blend in PPS for higher permeability (μr ≈ 95) and lower core loss at 600 Hz. Ready‑print FDM + 150 °C air cure.
Technical Specifications
Continuous Service Temperature: 150 °C
Magnetic Permeability: μr ≈ 95
Core Loss: ≤ 30 W kg‑¹ @ 600 Hz
Density: 5.1 g cm‑³
Thermal Conductivity: 0.8 W m‑¹ K‑¹
Key Applications
48 V e‑bike & quadricycle motors (2–8 kW)
Low‑voltage generators & PFC chokes
Rapid prototyping light‑EV drives
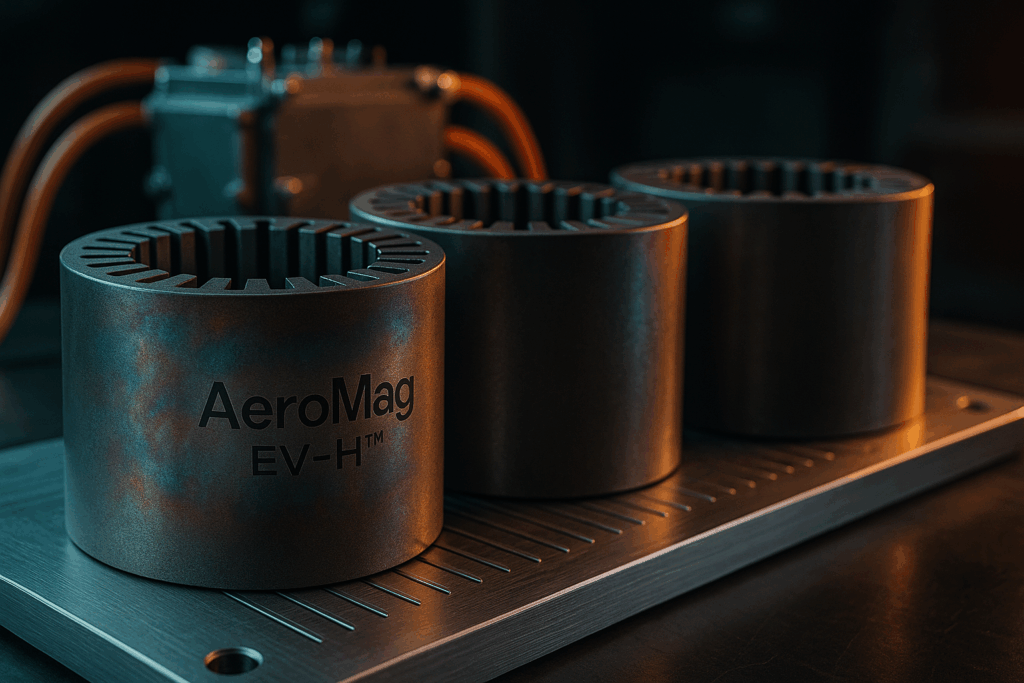
AeroMag EV‑H™
High‑Voltage Sintered Composite for 400 V Traction
Description: Designed for passenger‑car traction (50‑150 kW), EV‑H™ uses 64 wt % Fe‑Co V powder printed via DLP and fully sintered at 700 °C, achieving μr ≈ 150 and core loss ≤ 10 W kg‑¹ @ 400 Hz.
Technical Specifications
Continuous Service Temperature: 200 °C
Magnetic Permeability: μr ≈ 150
Core Loss: ≤ 10 W kg‑¹ @ 400 Hz
Density: 6.8 g cm‑³
Thermal Conductivity: 5 W m‑¹ K‑¹
Key Applications
400 V passenger‑car traction motors
Liquid‑cooled IPM & axial‑flux machines
Aerospace e‑propulsion up to 220 °C
• Reinventy Solutions is not responsible for comments, interpretations or re‑use made by third parties.
• All specifications are preliminary and may change without notice; shared links should therefore cite the original URL.
• This limited permission does not convey any licence to our trademarks, images or technical data beyond the context of the original page.
See the full Master Technology & Commercial Disclaimer .
Get Started
Contact our experts for info, insights or demo material.
Email: aeromag@reinventy‑solutions.ca
Phone: +1 778 404 0050
Legal Disclaimer
Accessing or using the information on this page constitutes acceptance of Reinventy Solutions’ Master Technology & Commercial Disclaimer.